In modern homes, granite countertops are popular. This beautiful natural stone is one of the most durable materials suitable for most building projects. Granite is a perfect option for countertops, backsplashes, and several other surfaces. Whether you are building a house or renovating, the use of granite will add natural elegance to your home. This guide gives you insights into how granite is mined and eventually turned into kitchen counters and different home surfaces.
Mining Granite is a large and massive operation that begins with finding granite deposits. The natural way of extracting the reserves is when granite deposits are exposed to open cast mining. Granite is then extracted from the mine. Granite mining is a complicated process that requires great expertise and equipment. Granite is usually boiled or cut and pounded into divided blocks and then lifted from the cranes to the earth’s surface into a nearby operating facility.
The material is transported with cutting equipment from the mine in large blocks that can weigh up to 10 tons. The stones are then cut into simpler working and useable sizes. Granite is charged in containers from the manufacturing plant and transported worldwide. As granite arrives, it is burdened with HGVs.
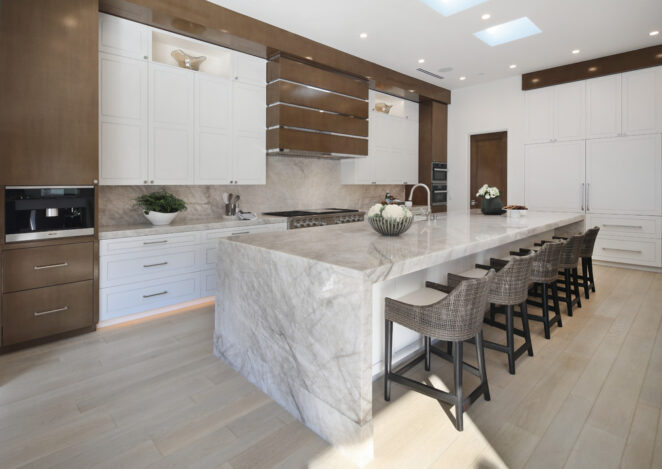
Inspection of the Slabs
As a natural product, stone also has features derived from this particular substance, similar to birthmarks in people. These include dry seams, black spots, resin-filled polyesters, pits and natural lateral vein, feldspar, and mica conglomerates (knots). Though the marks may make natural stone unique and beautiful, some extreme features may look like deformities and not impress the client. Stone experts will either improve the piece or use it for something else.
At this stage, the manufacturers inspect the slabs.
Creating a Template Layout
The sheet is laid out, and the previously produced templates are placed on the stem to ensure the best look of the vein texture and color. Templates designs ensure that the different countertops of your layout flow adequately. You want to ensure that your complete project’s overall flow will work, for instance, with an L-shaped countertop or an island that is parallel or perpendicular. A beautiful countertop is just that, a work of art that is made to impress. See our article on templates and seams for more information about the value of templates in your project.
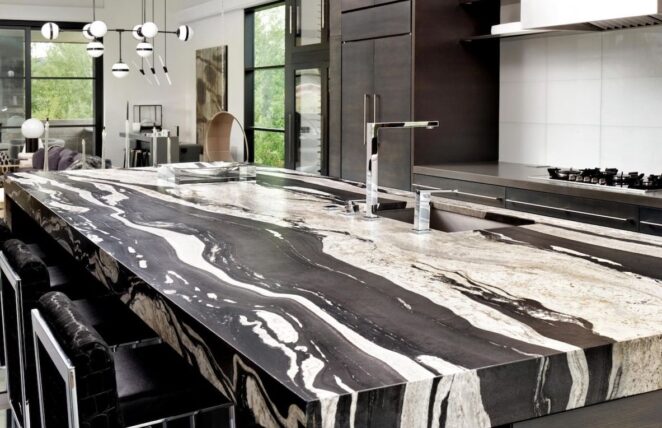
Cutting the Slabs
At this point, the stem is cut by a water jet or a bridge screw. Historically, the bridge saw has been the preferred weapon, but the saw jet has been a success in recent years. The advanced tool is configured with the parts. A manufacturer will then decide where to use the wastewater jet and the saw.
A feed rate of approximately 7 feet per minute cuts the bridge with a diamond-segmented blade. The water jet slices are cut at a pace of 1 foot per minute with high-pressure water and granite particles suspended in the water. Besides increasing efficiency, the water jet can cut circles, radius, or some complicated pattern, where the bridge cuts straight lines.
Fabricating
The cutouts for your under-mounted sink, cooktop, or holes are all made during this process of stone construction. The first move is to cut the stone to around 1/16 inch in dimension. CNC system is programmed to understand the size of the stones or the surface. The number-controlled computer pieces of stone can be placed on the table and worked together. CNC computer is designed to find the stones and what to do with each of them. As each stone has different features, a professional and experienced CNC machine operator is essential. It’s a challenge in which art and technology meet to create the best-finished product.
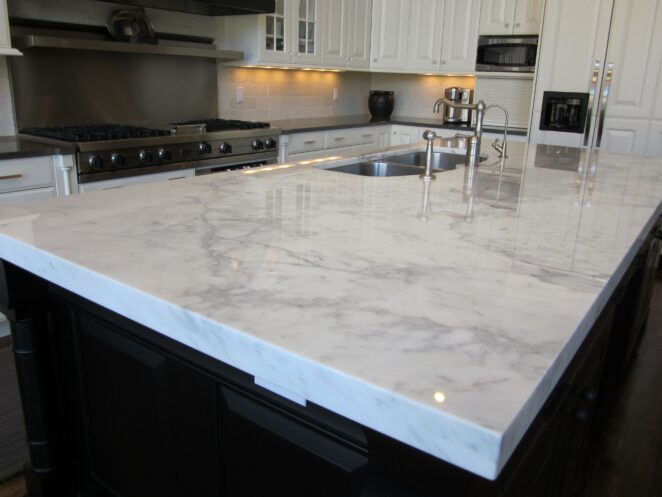
Strengthening of the stone
This task is exclusively for experts. Only specific manufacturers like Saturnia Travertini can handle the stone strengthening process. Cutting models will give you estones like the ones behind or in front of a sink or cooktop within granite rails. uThinner bits are by default not so solid as a broader stone surface. Experts conducted a study in the early 2000s in the Great Lakes to identify the best way to increase petric stems’ flexibility, significantly to strengthen this thin area.
Polishing
The polishing of the stone reaches the end of the process here. The face of the plate is already polished when the granite comes to the producer from the quarry. Granite texture at the manufacturer’s shop is typically not polished or modified. But it is the edge that needs polishing.
Seam Phantom
The stone soil is extracted during this stage, obtaining the best and nearest seam possible. This gives you a finished product where the seam can match well and not dwell on it.
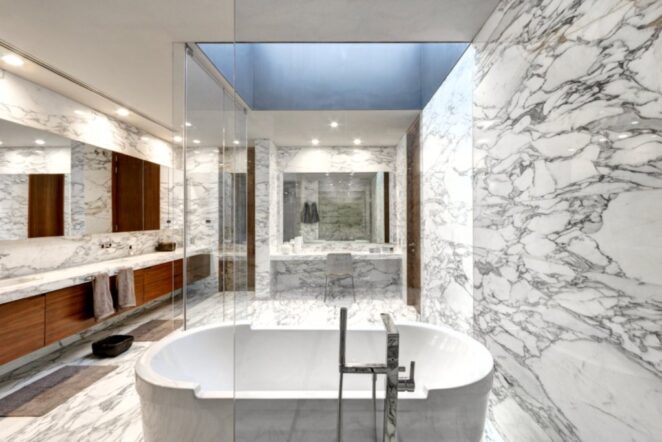
Sealing
Granite is 90 percent impervious. The rate goes to 97 percent by adding one coat of sealer. During this stage, both the edges and the stone face are screened.
Quality Control and Handling
The stone examination is the last process. Saturnia Travertini employs high quality and control checks to ensure that clients get the best products. At this stage, experts examine every stone to make sure that the product borders are uniform. The light should bounce off the edges consistently to add to the beauty of the piece. The color check is from various angles to produce a finished product ready for installation in any suitable part of your home.
Conclusion
Natural stones have stood the test of time. Buildings with these materials stand tall worldwide. You can use it in various parts of the house for both beauty and functionality. With the right products and correct expertise, natural stones will serve you and many other generations. This guide gives you an insight into the mining process and what happens when granite leaves the quarry.