Have you ever purchased a product that turned to be defective even just after a few days or even the first time you tried to use it? This usually happens because some products are exposed to external factors such as vibrations, humidity, and temperature that were not taken into account or expected when they were being designed.
For one’s product to stand out from the rest factors such as quality and reliability need to be taken into consideration. In today’s global market in which almost any product can be sold in every corner of the world, is it crucial that the design and development phase takes into consideration the different environmental factors the product will be exposed to? From cooler to warmer climates, corrosion, oxidation and many other factors.
In addition to these environmental conditions, it is also smart to take into account all the different stresses that the product may be exposed to during transport, packaging and other storage operations which can cause permanent damage or shorten the product’s lifespan.
Can your product withstand changes in climatic conditions?
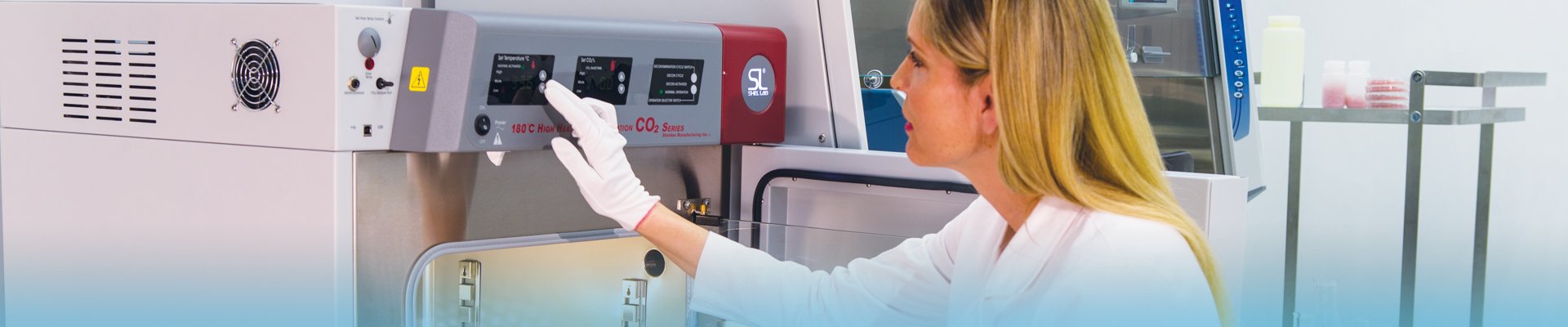
It is very likely that even from the first day of your product’s life it will be subjected to different stress factors such as solar radiation, high levels of humidity, climatic changes and vibrations. Are you wondering what needs to be done to avoid these kinds of things and ensure better product quality and reliability? The simple answer to this question is to use environmental test chambers.
A lot of companies during the Research & Development phase do a test on the prototypes of their product to check its reliability, stress resistance, testing characteristics or the behavior in different conditions. If these tests are not passed, the companies search for the defective component or the cause so they can correct the problem.
Different types of test chambers
The first environmental test chamber was built by Charles Conrad. He created the first test chamber by modifying a home freezer. His system could generate temperatures as low as -115°F. Since the invention of environmental test chambers, there have been many technological improvements that have allowed to serve companies with even wider purposes. Modern test chambers are not much more portable and can be even bought in miniature forms.
These test chambers are built for different purposes and have specific names such as sand and dust, altitude, salt spray, battery crush, temperature cycling, thermal abuse chambers.
If you are interested in test chambers, check out ugtx.com.
Altitude chamber
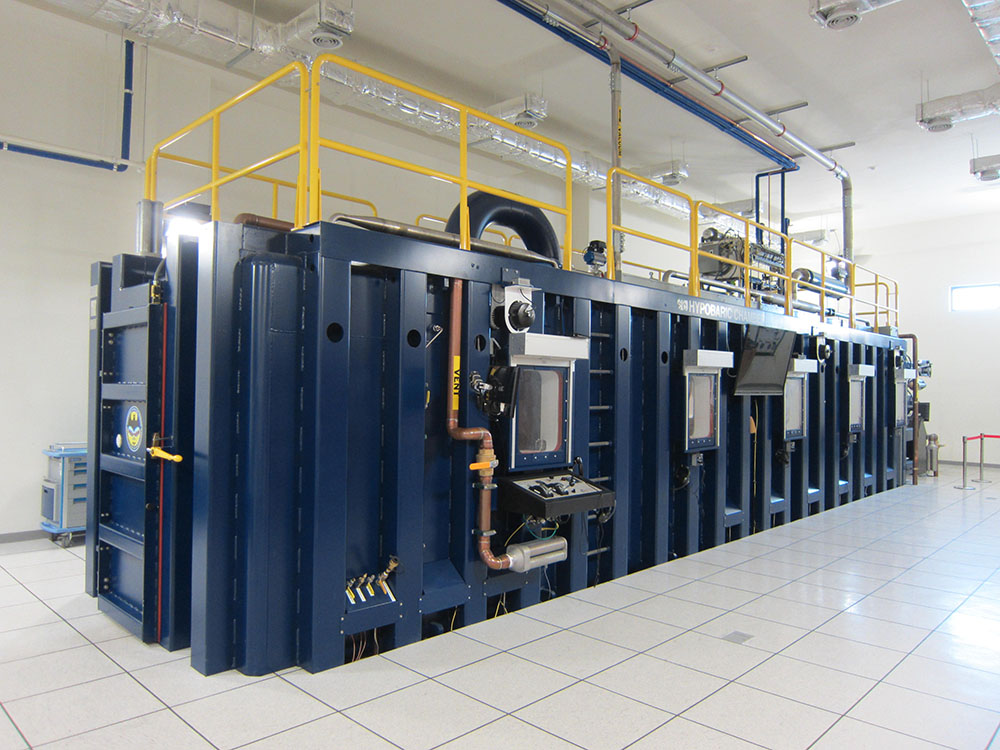
Hypobaric chambers or altitude chambers, test the effects on low-pressure on electronic, packaging and product that will probably be exposed to higher altitudes. They can also be used for human circulatory and respiratory response to altitudes up to 150,000 feet above sea level. Human testing is done for specialized activities and professions, like pilot and astronaut training.
Salt spray chamber
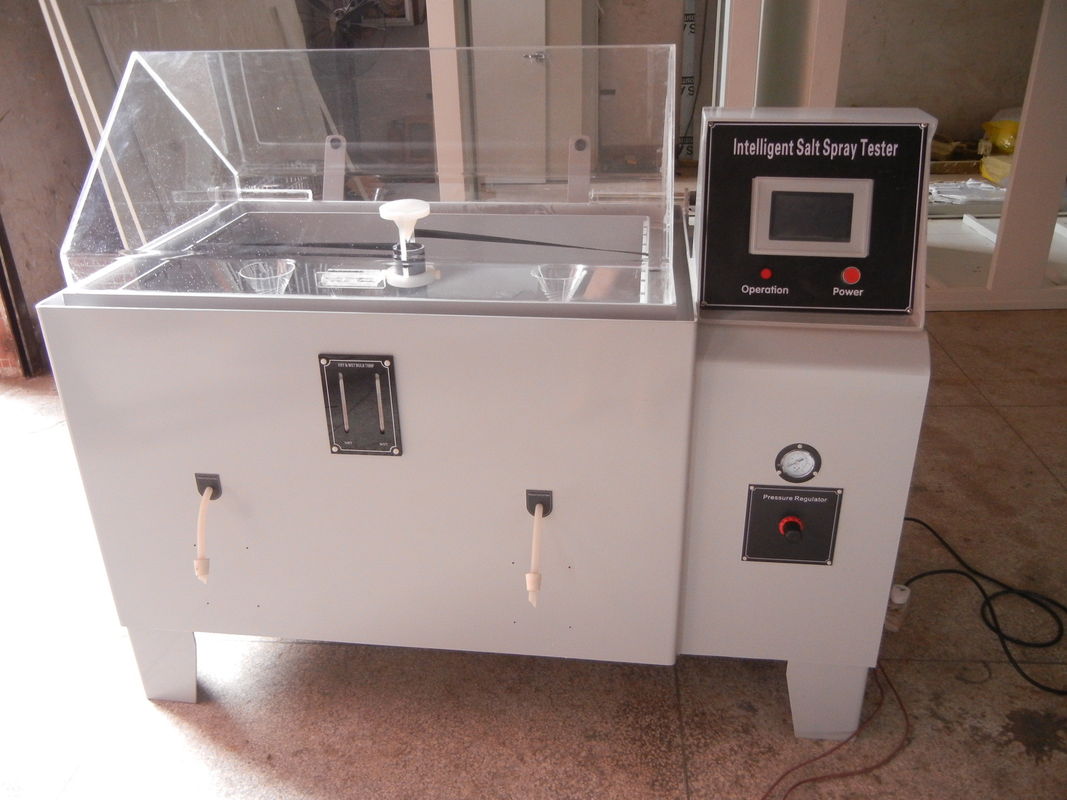
Fog chambers or salt spray chambers test corrosion resistance by introducing a hanging object in the chamber with a salty spray that creates a god. This process is usually pretty inexpensive and used by a lot of industries.
Vacuum chamber
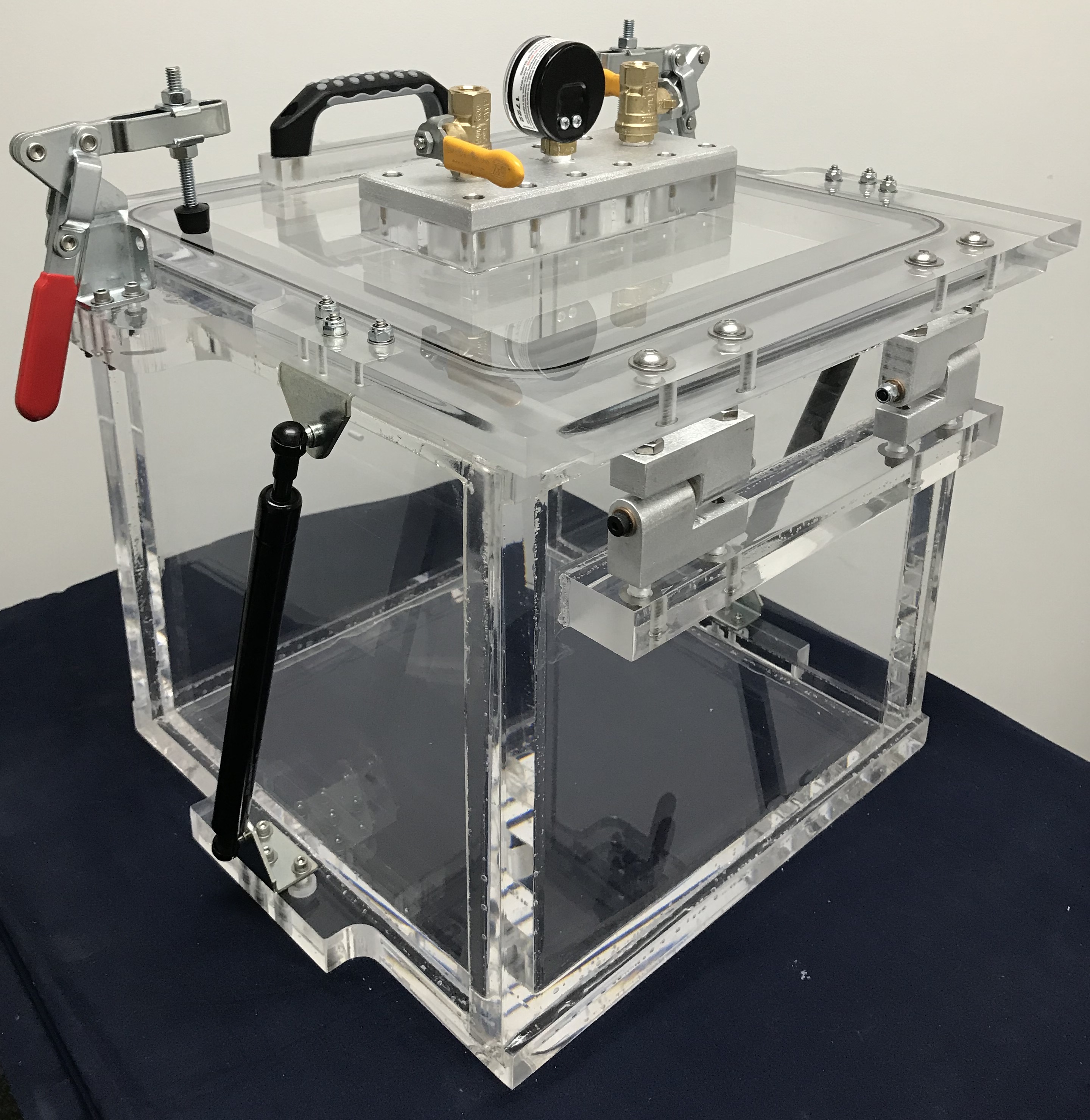
These are testing chambers where all matter has been completely removed. This is usually used for aviation and aerospace applications.
Humidity chamber 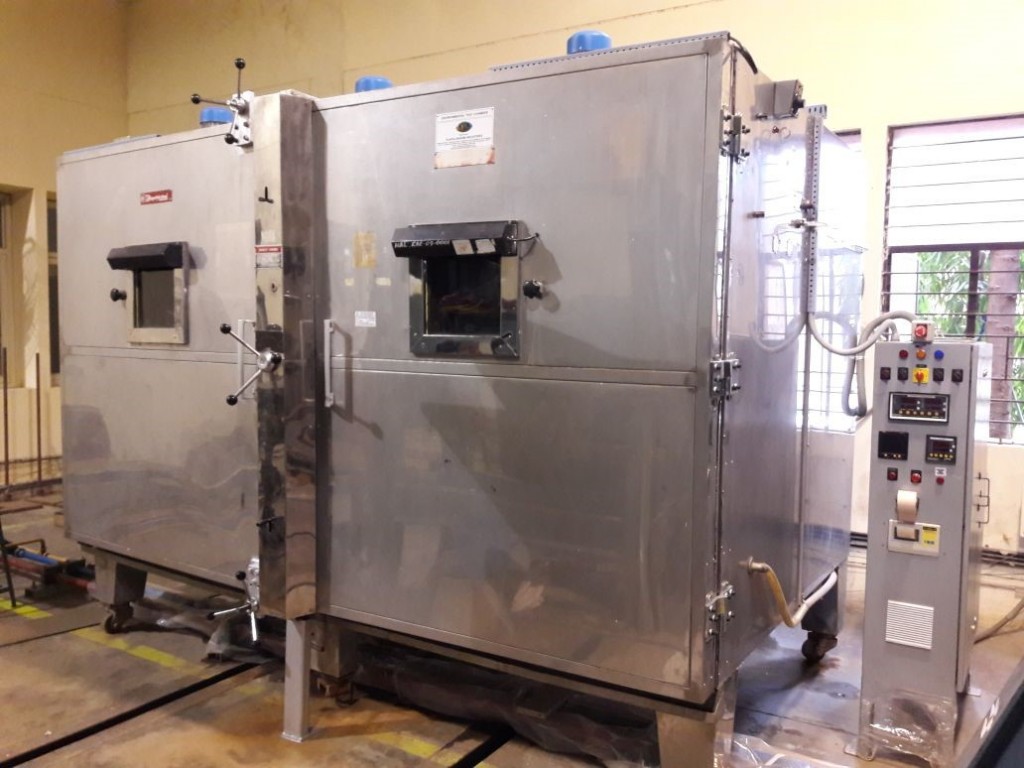
This is used to introduce a product with a variety of humidity conditions. This is mostly used for specific industrial and biotech applications.