Turbines operate in many ways. It is used to power the electric generators. The dynamo revolves around the same speed as the turbine. The turbines have been in service for more than a few decades. For some industries, turbines have become less efficient.
There has been an increase in the amount of research that is being carried out in turbine design. Since it is such a delicate piece of machinery that even a slight change in its pitch can affect its performance. In such a case, the power production can suffer to a high degree.
The efficiency of a turbine can be affected by the following things:
1. Corrosion:
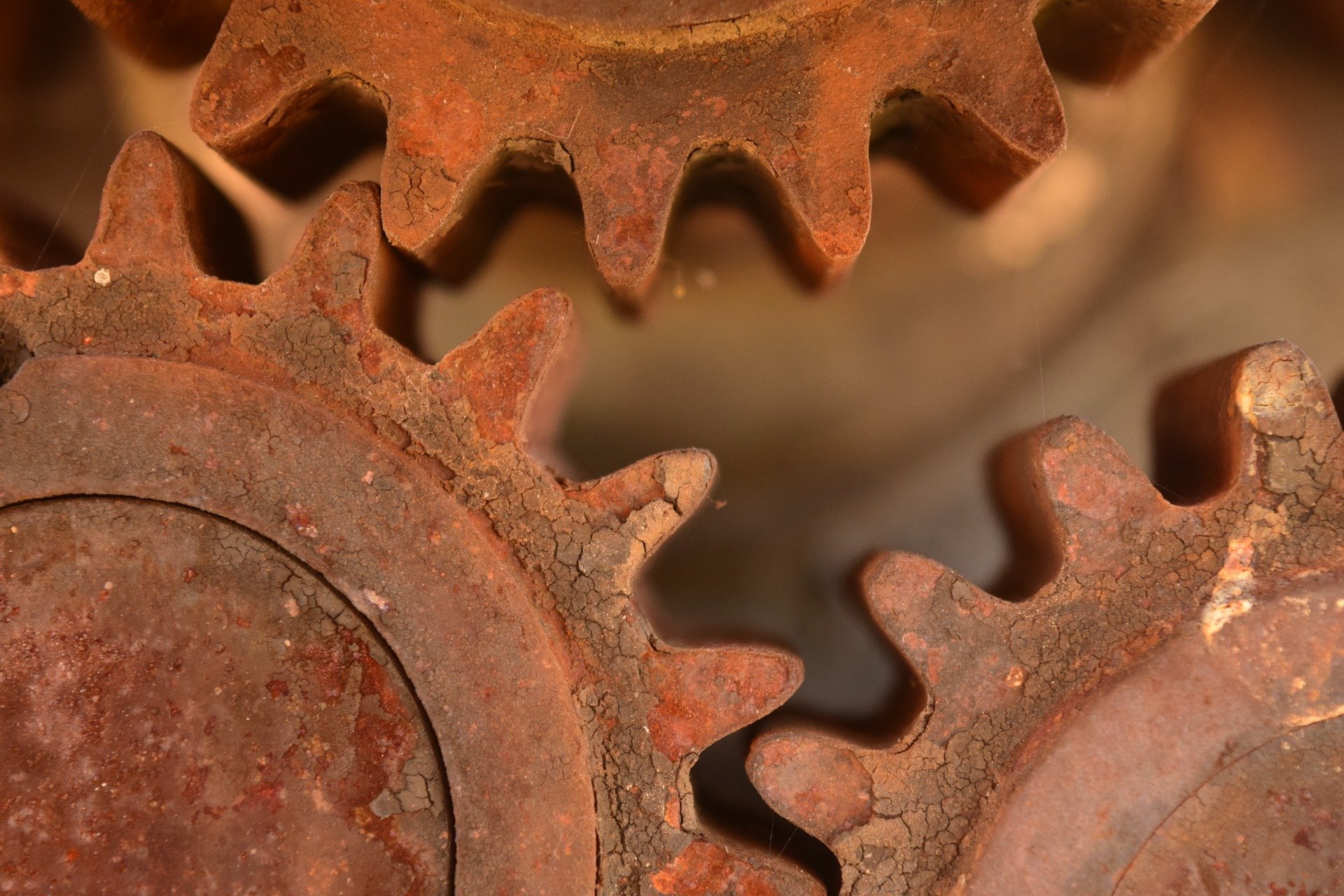
In a power plant, a turbine has to sustain a lot of steam pressure, which is why it is bound to corrode. The metal parts do not do well when they come in contact with humidity, mainly superheated steam. The turbine has to work under extreme temperature. It causes the turbine to be very sensitive in case the parts corrode.
When the metal comes in contact with steam, it starts to oxidize. It leaves the layer of metal covered in oxides. It starts to entrap more and more steam. Thus most of the pressurized gas escapes through the parts that become too unstable to support the pressure.
2. High-Quality Materials:
The turbine is made up of alloys of different types of metals. If you look closely, you may observe that they are built in such a way to withstand high pressure and heat. If that is not the case, then the walls and the turbofan will start to buckle under pressure. If you want to intensify the efficiency of the turbine, you should use high-quality materials.
The turbine can withstand the load of work for a much more extended period. It will save maintenance costs as well as keep the production running.
3. Result Oriented Design:
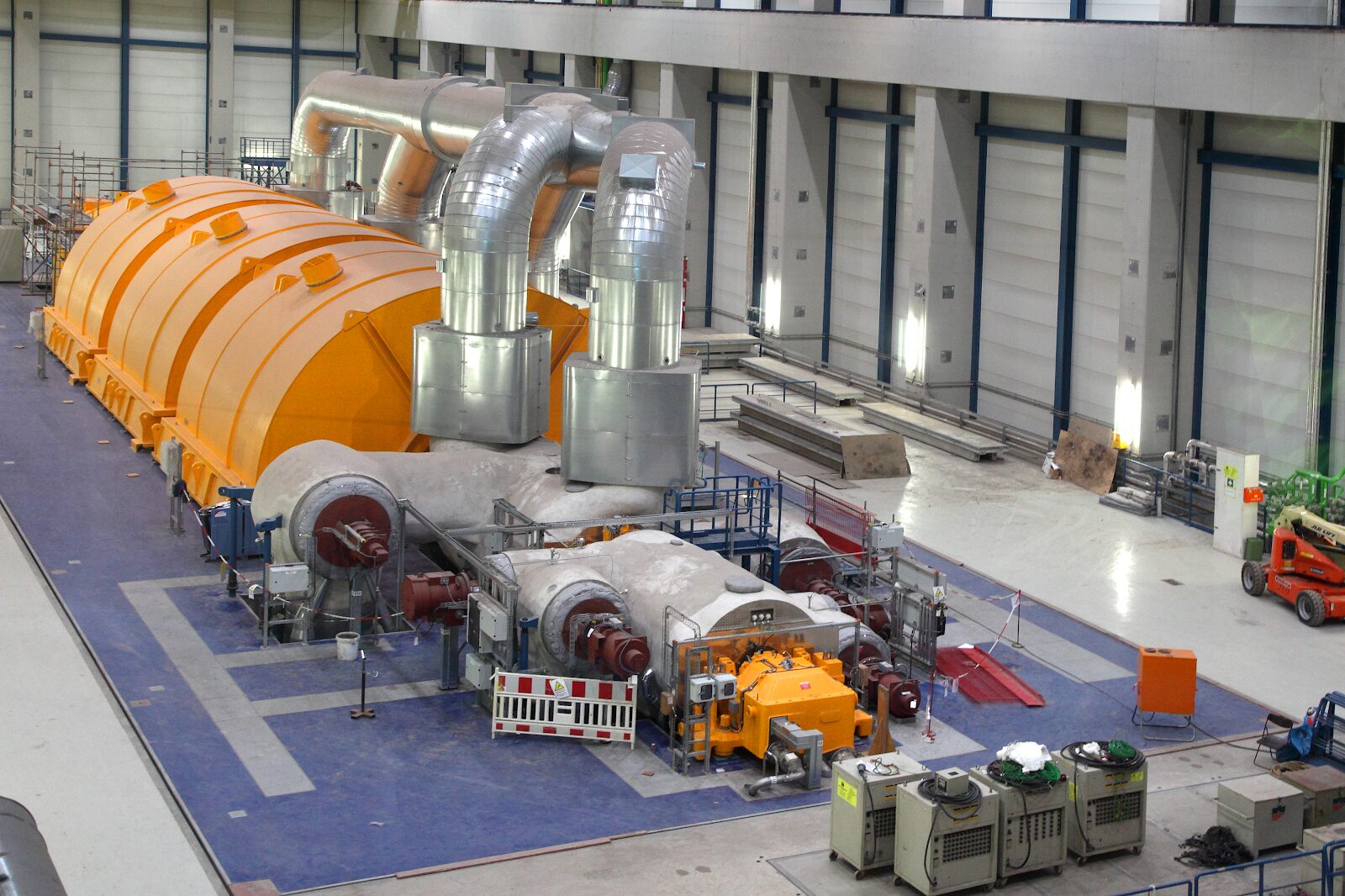
The design of the turbine can be changed to increase its output capability. As innovations are happening every year, you have to keep yourself up-to-date with unique designs. The turbine efficiency has reached 50 percent nowadays, thanks to routine research and experimentation.
The technologies after testing are carried out, can be implemented in your power plant. It can save you a lot of costs and give you more energy per your input.
Interestingly enough, just a little modification can have a considerable impact on productivity. Sometimes you do not have to change your old setup, replace certain parts. All of this translates into less cost for more profit.
4. Wear and Tear:
The components of the turbine are continually moving. There are a lot of moving parts, with some of them coming in direct contact with each other. It leads to friction, which results in chipping away of parts. The turbine immediately begins to wobble and lose its efficiency. It is highly unlikely for them to continue operating after a specific time.
Timely lubrication can keep the wear and tear to a minimum. You have to be vigilant not to overdo it as the lubricant will mix with the steam causing it to drop its high coefficient.
Although it is unavoidable by servicing you can prolong its life. However, after a particular time, it’s better to change the parts so that the efficiency can remain at its peak.
5. Skilled Operating Crew:
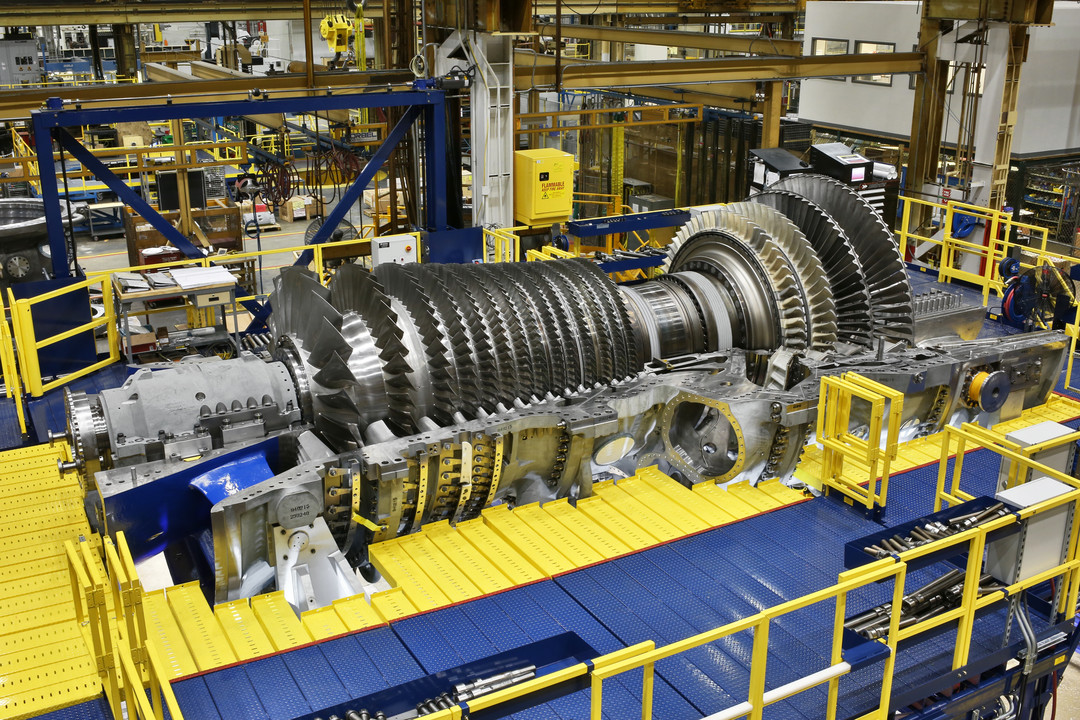
The power plant faces a lot of issues which they have to resolve daily. If you do not have experienced labor, then little problems can become big problems. A well-trained crew can maintain the machinery, giving it optimum performance.
The good thing about this is that you tweak the settings of the turbofan and the injection pipes according to the demand. So, if you feel like the output is dropping, the workers can immediately set on a task to get it right.
6. Maintenance:
If you want your machinery to work optimally, you will have to perform regular maintenance work. Since the turbine is operating under a lot of temperature and pressure, there is a lot of wear and tear. If you do check the equipment for cracks, then the chances are that the little tears in time will become unrepairable. It will lead to changing the chunks of machinery will be a costly operation.
The halt in production will be a big blow to the energy production unit as well as the consumers. So to avoid all that regular maintenance can keep the equipment running smoothly, giving you more leverage in terms of expenditure.
7. Installing Better Pipes and Valves:
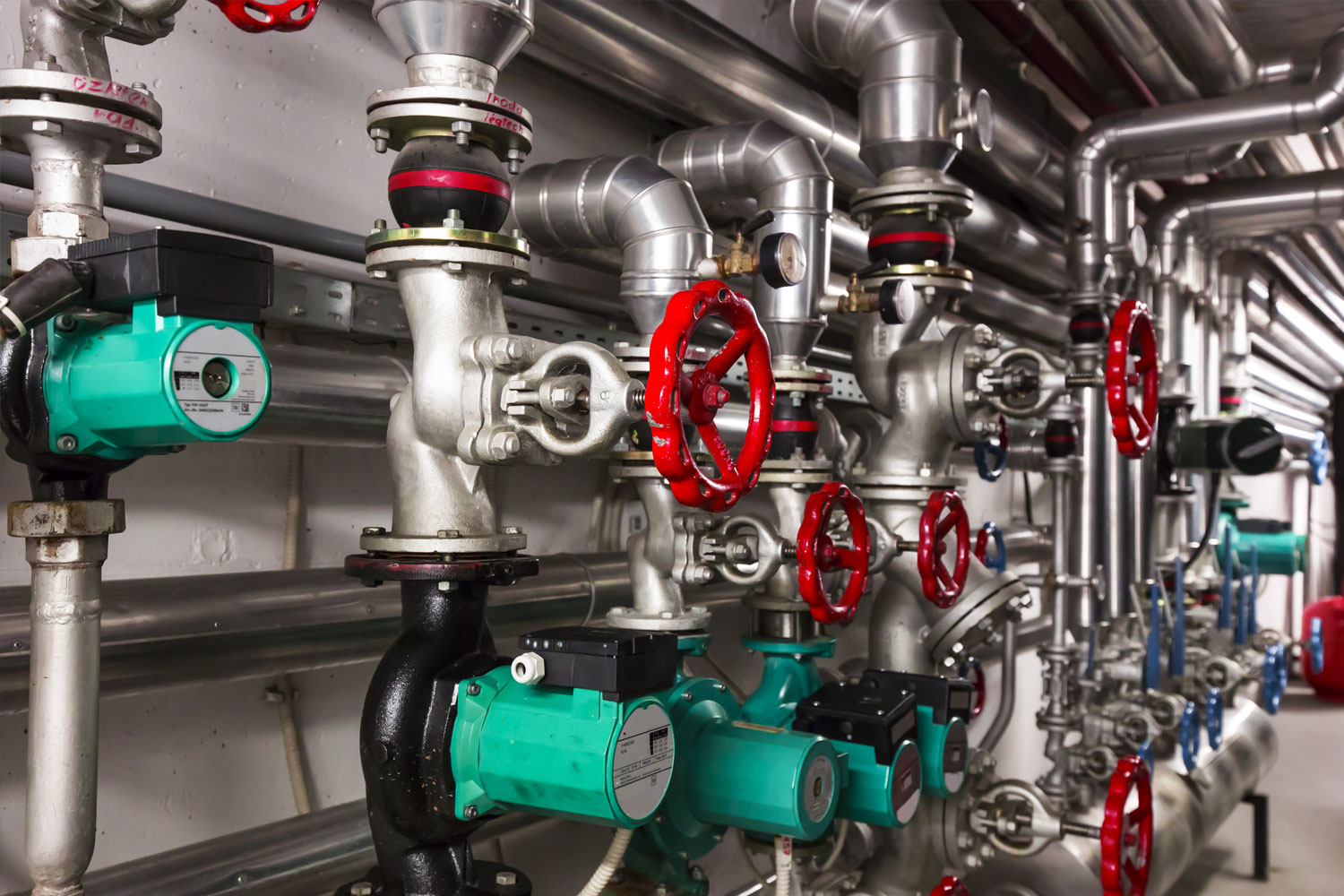
The operation of the turbine depends not on only significant parts like heat cap but also smaller pipes and faucets. It is imperative to inspect every little detail with great care. Since you do not have the extravagance of having a wide discrepancy between input and output, so every little bit counts.
If you feel that your present setup is not doing the job, then you should switch over to high performing valves. A great example is the various butterfly valves in XHVAL. These valves will not only help you maintain the pressure but also curb any line losses you face.
Conclusion:
The steam engine is made by the industries trying to make efficient machinery. They put in their best designers for the job. The engines are routinely under scrutiny to provide with the most optimal solution. Thus the improvement, however slight, can increase power availability.
The highly competitive market of today leaves little chance for error. Every turbine engine needs to be at its peak efficiency so that it can provide the necessary power.