Every day we tend to use plastic items, but we never really wonder how exactly they are made. Our phones use plastic cases, we use the bags of the same material when going to the supermarket, and even our keychain has some decorative items attached to it as well. They’re all made so carefully and in such large quantities, but we don’t seem to think about how fascinating that is.
If you make a comparison between the toys that are nowadays available on the market, and the toys that you used back when you were a child, you’ll notice that there’s a huge increase in build quality and design, as well as more attention to detail. Well, this is all thanks to the technological advancements in the plastic injection molding industry, and that’s exactly what we’re here to talk about today.
Plastic might not be the most favorited material at the moment, especially with all the pollution going on and the campaigns for using eco-friendly materials, but it still has huge importance in the industry. Today we’re going to talk about one of the best ways of creating items out of plastic, which is injection molding, so sit tight and let’s begin.
1. The efficiency of automation
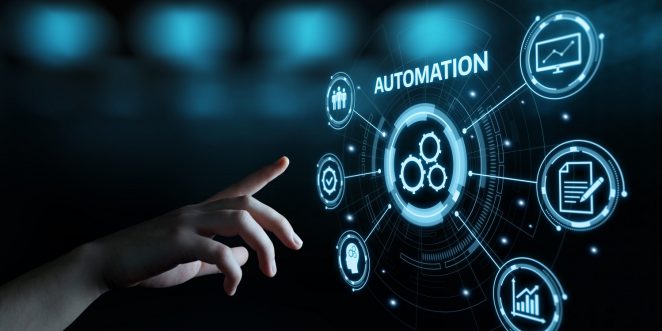
It’s more than obvious that machines are replacing people in almost all industries, but the injection molding field is something that benefits quite a lot from automation. In this environment, humans have very difficult and monotonous tasks, but luckily machines are here to replace them. Besides, we all know that the risk factor when it comes to making mistakes decreases by a lot when machines take over in the production procedure, and the benefits don’t stop there.
Not only that fewer mistakes are being made, but a lot of time is being saved as well, and over the long course, employers decrease their costs because they don’t have to constantly pay their employees. Sure, the initial investment for purchasing the machines is huge, but when you look at the bigger picture, it’s a great long-term plan.
2. Eco-friendly materials
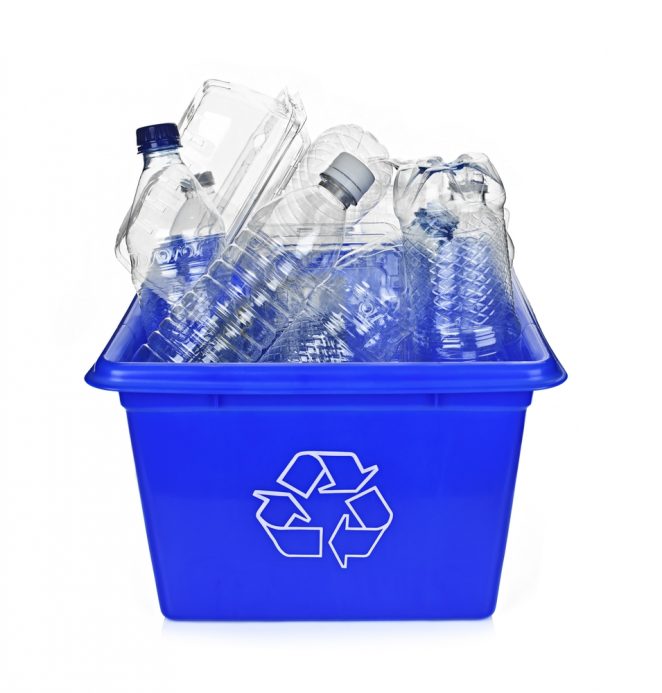
Just like we mentioned above in the article, the use of plastic is considered to be something that’s slowly becoming out-of-question, and it will probably keep happening until the pollution levels are brought back to “normal”.
However, recently there was a breakthrough advance which was also a challenge for a very long time in the molding industry, but after numerous tests and researches, most companies are finally able to start working with eco-friendly materials.
We’re not sure how businesses are going to shift in the next couple of years, considering that some countries even started banning certain materials with a high pollution factor, but the usage of eco-friendly ones is definitely a huge step forward for the entire industry. Also, if you are from China and you’re interested in contacting a professional molding company, feel free to visit qmolding.com
3. Microworks
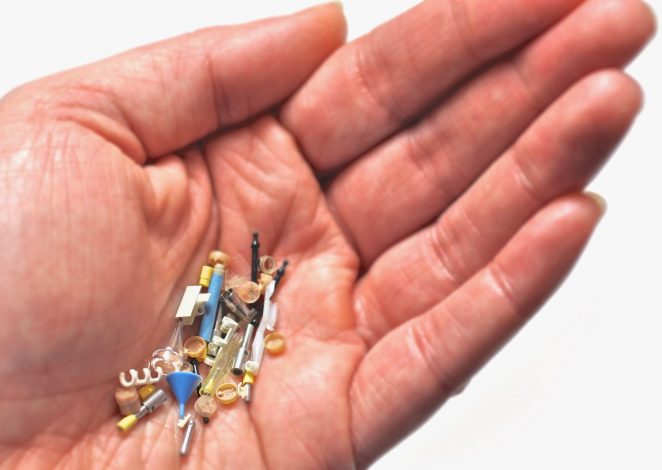
As time goes by, the designs of certain items are slowly becoming more and more complicated, meaning that the industries have to find ways of making them without sacrificing some of the quality. Thankfully, this can be achieved through something that’s called micro-molding.
Although it’s a “buzzword” that people tend to throw around a lot, it’s actually a very large step in the entire industry, and it can help the manufacturers produce things that are on the microscopic scale. Imagine how helpful this can be when it comes to the production of certain parts for medical equipment and other useful things that can save the lives of many people.
It’s not very easy to identify if there are any errors in such small parts, but there’s an efficient way of doing that as well.
4. Less-consuming machines
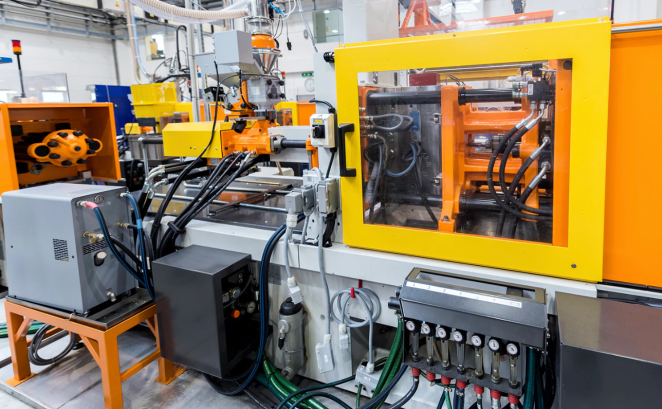
Energy consumption is a huge topic nowadays, and most of the time people really tend to give manufacturers “the bad look” when they mention how much they’re spending for their operations. Thankfully, as time slowly passes by, the machines used in the injection molding field are becoming more advanced, and they tend to spend a lot less energy than the previous models.
You might think that swapping out machine models and equipment is not as frequent in the industries, but that’s not really true. Energy consumption is a huge factor in the costs that the owner of a certain factory has to pay, and since they are all interested in making a profit in the long-term, they always give their best to have the most energy-efficient machines.
Every few years, a factory does a full replacement of their machinery, because the progress that’s being made across the models is pretty significant.
5. Automatic quality control
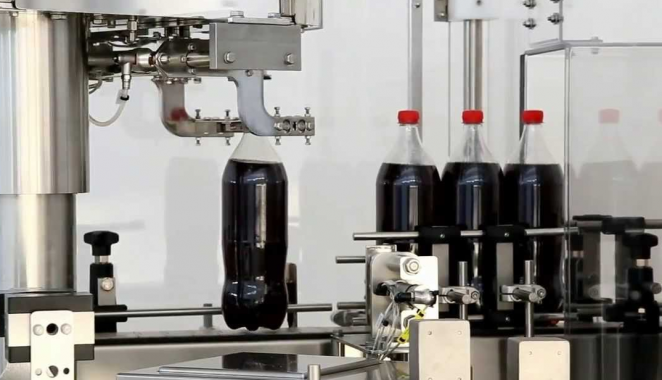
Imagine how much work one person has to go through if they are working in the injection molding industry, on a position that requires them to do thorough quality-control for each and every piece that’s being produced. There’s just so much to be checked, and such a huge room for errors. On top of all this, the employer has to pay hundreds of workers and that’s just not really beneficial for the long-run.
Thankfully, inventors came up with a lot of solutions that allows machinery to do the quality-control part on the same parts that it produces, meaning that the room for error is drastically reduced. Also, you get to replace a pretty “annoying” position that’s very tiresome with a robot that doesn’t mind checking thousands of pieces on a daily basis. Of course, there’s still some improvement that needs to be done, but progress is on its way and it’s a large step for the industry.
Conclusion
A lot of our consumer items that we use on a daily basis are made in the plastic injection molding industry, and we’re not even aware of it. However, this industry is not only responsible for creating things such as phone cases and key-chains, but it has a much larger purpose as well. Recently, there have been numerous examples that point out that the parts created in this field are used for many useful devices and machinery, such as the ones used in medicine. Thankfully, this industry is constantly evolving, and with some of the latest trends that we listed above, we can expect even better products in the future.